Case Study
- Case Study
- Bombardier
Integrating Technical Documentation and Illustrated Parts Catalogs with the Manufacturing Suite
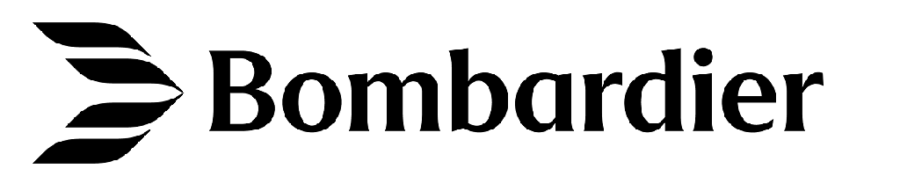
About Bombardier Transportation
Bombardier Transportation was a Canadian-German rolling stock and rail transport manufacturer and one of the world’s largest companies in the rail vehicle and equipment manufacturing and servicing industry. It produced a wide range of products including passenger rail vehicles, locomotives, bogies, propulsion and controls. The company was acquired by French manufacturer Alstom on 29 January 2021.
In Brief
Challenge
The publications team faced
- Labor-intensive management of large, intricate technical documents, Illustrated Parts Catalogs, maintenance documents, and training.
- Deliverables coming from various sources.
Yet, they could not get executive buy-in for transitioning to a structured authoring system, as traditional benefits like efficiency and content reuse were not persuasive enough.
Solution
The XDocs DITA CCMS, the Manufacturing Suite, and the XDelivery Documentation Portal achieved executive management buy-in by providing a solution that offers
- A single database from which to create, manage and publish technical documents, IPCs, parts information, and maintenance schedules.
- The ability to ingest and integrate BOM content from ERP systems and parts diagrams from CAD systems, then publish to PDF and HTML
- Quick and easy creation and publication of online IPCs that are linked to parts ordering systems and precisely customized to a particular BOM.
Benefits
The solution could increase after market parts sales by 10%, a significant increase in revenue, while reducing support costs.
The Challenge
Bombardier Transportation (BT) had a problem. Documentation for their rail vehicles was very complex, difficult to manage, and labor intensive. Documents were created in traditional authoring tools such as Microsoft Word and delivered in a technical documentation portal called an Interactive Electronic Technical Manual (IETM). The IETM comprised large technical documents as well as Illustrated Parts Catalogs (IPCs), maintenance schedules, and training. All of these deliverables came from different sources, and were typically delivered as PDF documents.
For years, the publications management team searched for a better solution. Their research led them to the conclusion that they needed to move to structured authoring with DITA and a CCMS. However, they could not get management buy-in for a business case based on the classic benefits typically cited for such systems in areas such as authoring efficiencies and content reuse.
The Solution
BT’s publications management team searched for a system for seven years. The breakthrough came in discussions with Bluestream management, when they realized that the greatest value would be realized if both parts information for IPCs and documentation came from a single database where BT could manage and publish technical publications, IPC parts information, and maintenance schedules.
A unified vision to create, manage, and publish a next generation IETM by using a single database for creation and management of technical documents, IPCs, and maintenance schedules allowed the Bombardier Transportation publications management team to get executive management buy-in and move forward.
Bluestream’s Manufacturing Suite module, which ingests and integrates parts Bills of Materials (BOM) content from ERP systems and parts diagrams from CAD systems, was the key.
The Manufacturing Suite
- generates DITA content from the BOMs and parts diagrams
- imports the content into the XDocs DITA CCMS
- automates publication to PDF and HTML.
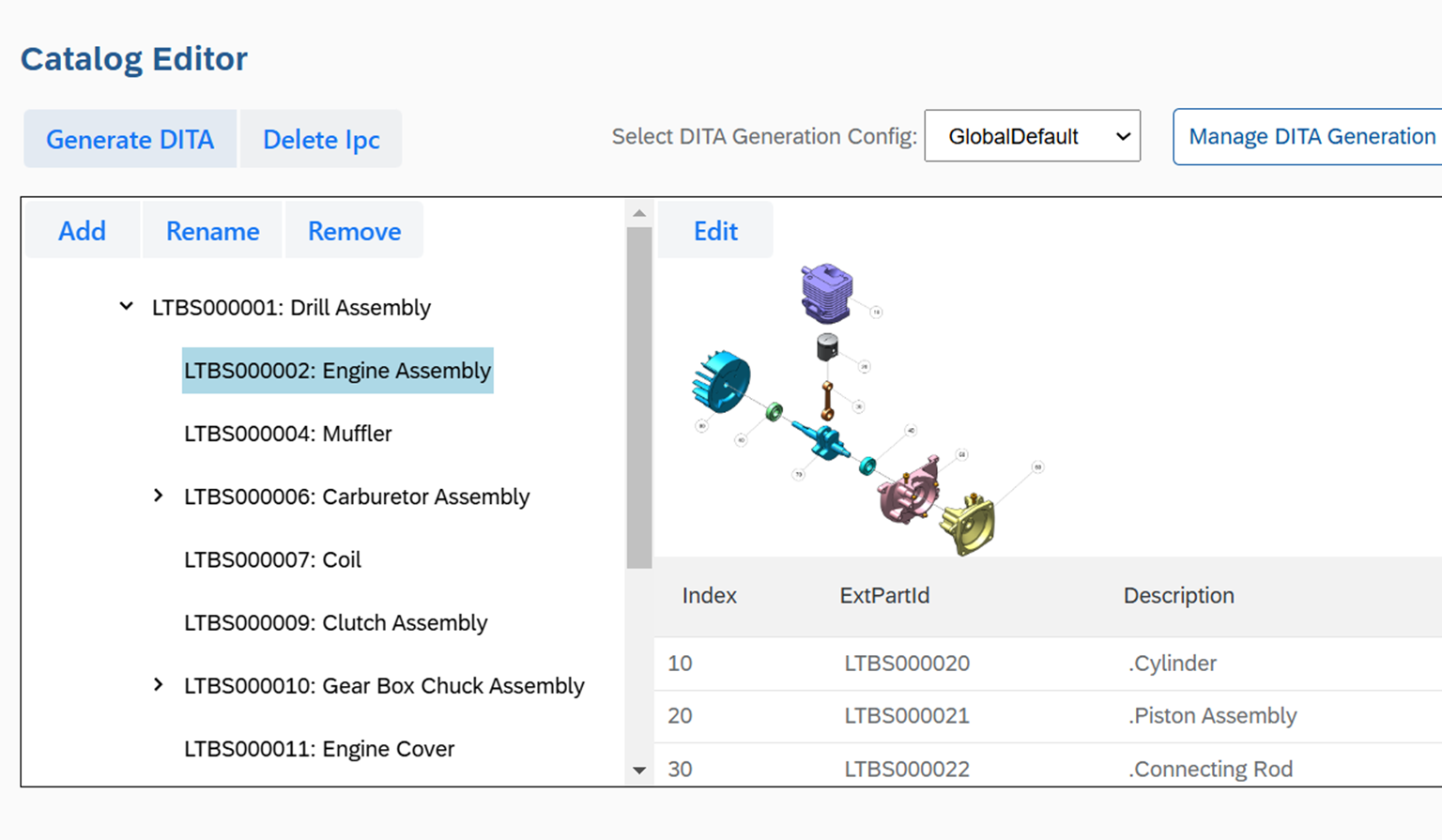
The HTML can be posted directly to the XDelivery Documentation Portal as an online IPC with integration to parts ordering systems. The IPC is precisely customized to the project BOM. This could increase after market parts sales by 10%, a significant increase in revenue, while reducing support costs.
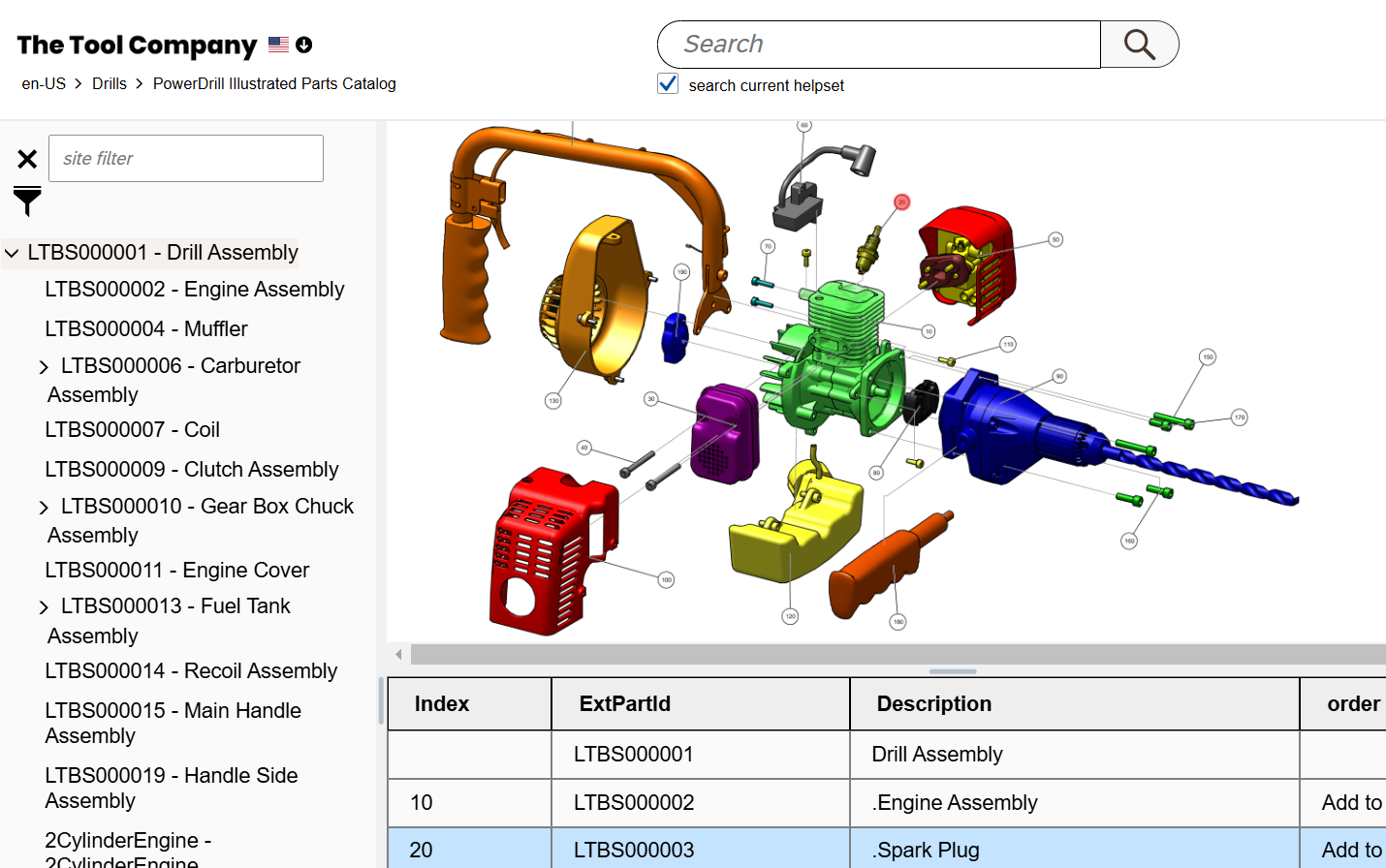
The Benefits
By moving to DITA and the XDocs DITA CCMS, BT could manage all technical documents in the system and realize benefits in content management, reuse, metadata management, workflow, review, and more.
In addition, parts content is available for insertion directly into technical publications through the DITA authoring interface. Through careful data modeling and sophisticated output processing, maintenance schedules could be authored as individual topics in different locations within the maintenance manual, then auto generated as separate publications.
Going forward
Integration of parts BOMs with technical documentation is the future of content management in companies that make complex machines. The XDocs MI solution enables IPC generation specific to the project’s parts configuration. Publication to XDelivery Documentation Portal provides a unified experience.
In Brief
Challenge
The publications team faced
- Labor-intensive management of large, intricate technical documents, Illustrated Parts Catalogs, maintenance documents, and training.
- Deliverables coming from various sources.
Yet, they could not get executive buy-in for transitioning to a structured authoring system, as traditional benefits like efficiency and content reuse were not persuasive enough.
Solution
The XDocs DITA CCMS, the Manufacturing Suite, and the XDelivery Documentation Portal achieved executive management buy-in by providing a solution that offers
- A single database from which to create, manage and publish technical documents, IPCs, parts information, and maintenance schedules.
- The ability to ingest and integrate BOM content from ERP systems and parts diagrams from CAD systems, then publish to PDF and HTML
- Quick and easy creation and publication of online IPCs that are linked to parts ordering systems and precisely customized to a particular BOM.
Benefits
The solution could increase after market parts sales by 10%, a significant increase in revenue, while reducing support costs.
Realize the potential of your content
The XDocs DITA CCMS, the XDelivery Documentation Portal, and the Manufacturing Suite add value by streamlining documentation processes, creating efficiencies, improving content quality, and enhancing customer experience.