Case Study
- Case Study
- Warehouse Equipment Manufacturer
Warehouse Equipment Manufacturer (Anonymous Client)
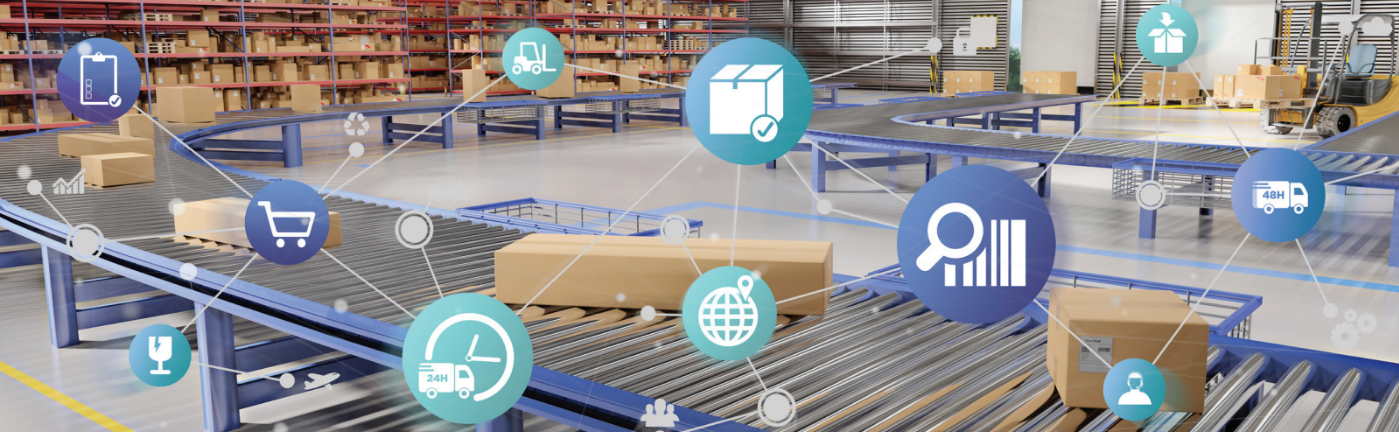
The Challenge
Bluestream’s client is a major player in the global fulfillment and warehousing industry. They create customized order fulfillment solutions, including warehouse parts handling equipment, for hundreds of sites. While they create generic designs, every warehouse uses different combinations and variants of parts. Creating and delivering the right information for each site was overwhelming.
Parts and service content was hard to manage. Generic parts and service content was written in MS Word and manually merged with illustrations that identified parts. The content was then delivered over the web in PDF format. Sometimes content was manually customized for specific sites.
Creating content was inefficient and time consuming, and the service documentation was hard to use — making it difficult to maintain machines and to identify and order replacement parts. Updating information was slow and labor intensive — changes were manually detected and inserted. The documents were static and almost impossible to keep up to date.
As with any manual update process, something could be missed and errors could creep in. Additionally, orders of incorrect or outdated parts caused delays, expense, and frustration.
The Need for Change
Bluestream’s client needed a new approach to efficiently generate site-specific parts and service content, automate IPC (Illustrated Parts Catalog) generation, and provide timely, accurate content to their customers with an integrated shopping cart experience.
This would streamline the parts ordering process, increase revenue from after-market parts, and reduce support costs.
“Bluestream’s client can now provide Illustrated Parts Catalogue (IPC) and service documentation to their customers based on exactly what was supplied and installed. This makes for much easier field service support and maintenance as well as correct parts ordering ”
Anonymous Client
Bluestream Content Solutions
The Solution
IPCs (Illustrated Parts Catalogs)
IPCs allow engineers to easily identify a particular component utilising General Assembly, Sub-Assembly and exploded component drawings.
When delivered electronically an IPC can be easily linked to a fulfilment system. This enables engineers in the field to instantly request replacement parts directly from the manufacturer. IPCs reduce the chance of the wrong part being ordered and create a valuable revenue stream.
CCMS/Authoring Environment
XDocs DITA CCMS is an enterprise class component content management system. Embracing open standards where possible and designed for flexibility, it has been deployed all over the world.
Moving to structured authoring and DITA has brought immediate benefits. Using XML separates the content from the formatting, and allows for content to be published in various formats including PDF for print and XHTML/HTML5 for online.
It is now much easier to reuse content, and significant savings have been made on localization.
Automated Image Processing
With XDocs Manufacturing Suite, Company A can import an ‘as-built’ BOM from their ERP system for any customer site. CAD diagrams are automatically processed to link call-outs from parts in the illustration to the BOM content.
Dynamic publishing
XDocs Manufacturing Suite merges the BOM content and diagrams to dynamically publish customer and site-specific Illustrated Parts Catalogs to the XDelivery Interactive Service Documentation Portal.
These IPCs have shopping cart functionality which can be linked to the parts ordering system and the CRM system.
Unifying parts & service information
Parts data is also available for use in other documentation types, for example installation and maintenance manuals. As a result, parts data in the service documentation is linked directly to the IPC on the service portal. Since parts information is now managed in a content creation engine, it is also available for integration into training materials.
Multilingual parts ordering site
XDocs DITA CCMS integration with Translation Management Systems enables Company A to manage parts content in multiple languages and publish to a multilingual parts ordering site.
Improving the customer experience
When a customer, or technician is on site, spare parts information is provided via the Interactive Service Documentation Portal for their as-installed system. Using IPCs, they can easily identify and order the exact parts needed through their online platform via a laptop or mobile device.
IPCs make identifying the correct part a simple task
Timely, simple content updates
For quick updates, catalogers can add or change content in the Catalog Editor before publishing or updating the IPC. For more comprehensive changes, the BOM can be reimported. XDocs Manufacturing Suite automatically versions all content, allowing auto- detection of changes.
Simple reviews
XDocs Manufacturing Suite also supports browser-based review of all content prior to publishing.
SMEs (Subject Matter Experts) can be easily incorporated into review cycles using XDocs WEX – a simple to use browser based review and collaboration application.
XDelivery Service Documentation Portal
Bluestream’s XDelivery Documentation portal links directly to the core XDocs database. Customers can make Technical Documents available to their customers and engineers according to permissions.
Benefits
With XDocs DITA CCMS & XDocs Manufacturing Suite you control the flow of ‘Service Information’ from Engineering to Fulfilment:
In Brief
Challenges
- With different combinations of parts for every warehouse, creating and delivering the right information was overwhelming.
- Creating parts and service content in MS Word content was inefficient, time consuming, and hard to manage
- Service documentation was hard to use, making it difficult to maintain machines and to identify and order replacement parts.
- Updating information was slow and labor intensive
- Documents were static and often out of date.
- Errors crept in to manual processes.
- Orders of incorrect or outdated parts caused delays, expense, and frustration.
Results
- Streamline the service documentation process, from creation through review, approval, and release
- Automate processes for parts management, eliminating errors
- Improve the quality and usability of service documentation
- Efficiently generate site-specific parts and service content
- Automate IPC (Illustrated Parts Catalog) generation
- Provide timely, accurate content to their customers with an integrated shopping cart experience.
- Streamline the parts ordering process
- Increase revenue from after-market parts
- Reduce support costs
- Audit trail – what was changed, when’ by who.
- Instant comparison between versions.
- A streamlined workflow for producing integrated service documentation.
- Rapid information updates to all output formats i.e. IPC, Doc, Maintenance Schedules.
- Helps ensure data consistency and integrity.
- Eliminates system redundancy.
- Build fully customizable Web-based Delivery Portals.
- Enhance the end user product experience
- Create better documentation faster, reuse content with confidence and update information with ease.
- Create precise customizable Illustrated Parts Catalogs for each customer site.
- Build IPCs, Maintenance Schedules, Installation Guides etc. and localize them to any language.
- Increase parts sales and reduce errors in parts ordering.
- Make service engineers, catalogers, technical writers and service parts managers more productive.
- Full control of the information flow
Realize the potential of your content
The XDocs DITA CCMS, the XDelivery Documentation Portal, and the Manufacturing Suite add value by streamlining documentation processes, creating efficiencies, improving content quality, and enhancing customer experience.